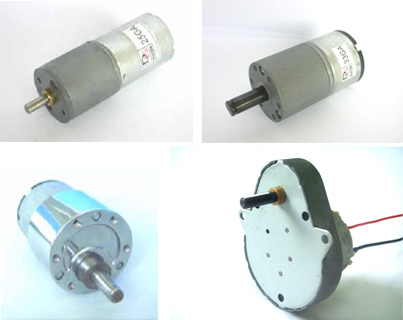
Gear Motors
The following factors affect the durability, performance and efficiency of gear motors:
Environment of use. Inappropriate environmental temperatures and high humidity can shorten the life of an AC or DC gear motor. While in use, the ideal temperature range for a gear motor is generally between 10 and 60 degrees Celsius. Environmental relative humidity shouldn’t exceed 85 percent.
Load conditions and impact loads. When a load exceeds a gear’s rated torque, the wear and tear makes the part increasingly inefficient. Exceeding the permitted thrust or overhang loads can also have a negative impact on a gear motor.
The gear motor’s operation. Mode of operation, frequent starting, reversing the turning direction momentarily and long-term, continuous operation can all shorten a gear motor’s life span.
Using the output shaft for forced turning. When you do this, the motor turns into an electrical generator and speed-increasing mechanism, which can damage the gears and other internal parts of the machine.
Pulse drives. Short breaks, PWM controls and counter electromotive force affect a gear motor’s durability.
Using nonstandard voltage instead of the recommend voltage.
Storage. Store gear motors in a location whose temperature doesn’t exceed 65 degrees Celsius, with low relative humidity and no materials that generate toxins or corrosive agents.
To learn more about increasing the longevity of a DC or AC gear motor, or for help finding the right one for your needs, contact Sinotech.